Product yields (the percentage of the spheroids produced in a batch that are within the size range required) will never be 100%.
However, it is possible for you to achieve yields of greater than 98% if your formulation, process parameters and the equipment used are optimised. Formulation and process parameters are outside the control of Caleva, but the quality of the equipment we can offer you is our direct responsibility and concern.
If your yield is 1% or 2% lower in each batch as a result of using lower quality equipment, you could be unknowingly suffering from a significant loss of income over the lifetime of a product. To obtain the highest possible yield, the equipment you use should be manufactured within tolerances that are as tight as possible. The manufacture and design of the disc pattern in a spheronizer is crucial for keeping your usable yield percentages as high as possible.
An example of how equipment can vary between manufacturers is shown in the pictures below.
The first disc is not manufactured by Caleva but is available from a low-cost supplier who is present in the marketplace. The second disc is manufactured by Caleva, and the quality difference is easily seen.
Uneven, poor quality disc cut pattern not from Caleva ...
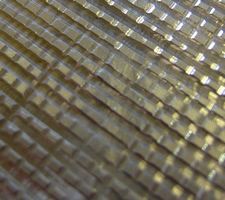
-
This is a disc pattern that has been cut by a lower cost manufacturer. You may be keeping costs low in the short term by purchasing lower cost equipment, but with low equipment quality like this your income will be reduced severely as time goes on. This makes the lower cost machine considerably more expensive over time.
-
The uneven pattern suggests an uneven spheronization action on the extrudate leading to higher variability in your spheroid size range. This wastes large amounts of your product, which you have to spend time and money to dispose of. These small daily losses can total a significant amount over the lifetime of your production.
-
If you are looking to use your spheronizer long into the future, then a disc like the one above will cause a continuous but unseen drain on your income. Not only will you be creating additional work, but you will also be losing money that in the long run will cost you more than buying reliable quality equipment from the start.
Even, high quality disc cut pattern from Caleva ...
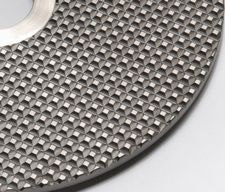
-
This is a disc pattern cut by us at Caleva. Due to the uniform pattern cut into our discs, you will be able to produce the highest percentage of usable yield possible. This will keep your long-term income as high as possible to get the most value from your product and production equipment.
-
A completely even pattern suggests an even spheronization action on the extrudate leading to lower variability in your spheroid size range. With this consistency your waste product is kept to a minimum. This could be extremely important, especially if your product is expensive.
How might this effect you?
Consider the total cost over the full life cycle of a product. Imagine you’re using a spheronizer to produce a product worth £10 per kilo (a low value product) over a 10-year period.
Your spheronizer produces:
- 50 kg per hour
- For 8 hours a day
- 5 days a week
- 40 weeks per year
If your spheronizer has a reduced usable yield of only 5%, it would mean a reduction of income of £40,000 every year. Over a 10-year product lifecycle this would equate to a loss in income of around £400,000.
What is the real cost of low-quality equipment?
Our pelleting equipment has the potential to maximise your usable yield.
For more complete information on our pelletization range, or any of the specific items mentioned above you can either: -
- Chat directly with us using our “Online Chat”
- Or talk to us directly via email: info@caleva.com
Leave A Comment