There is no simple answer to this question as it depends on the characteristics of your formulation and the size of the pellets you require.
One of the key factors (but not the only factor) that determines the diameter of the final dry pellet is the diameter of the hole in the extruder die. For example, if you are trying to make a pellet of 1.0 mm diameter then you should use a hole of the same diameter in the die plate as a starting point. If you want your pellets to be about 0.8 mm in diameter, then you should consider a die hole diameter of about 0.8 mm. For a pellet requirement of 1.5 mm diameter you should consider a hole diameter of about 1.5 mm and so on.
Close-up of the axial configuration on the unique Variable Density Extruder from Caleva
Another factor to consider before you make a purchase decision for your extruder is that it is always preferable if your extruder (of the modern extruder design) gives you the following options:
- The ability to acquire and use dies with holes of different diameter
- The ability to acquire and use the dies with the diameter you want and also with an option, in each case, to have hole depths that are different. Both factors are important because they allow you to examine the possibility to change the density (and not only the diameter) of the product produced. This is another key factor that can influence your R&D programme and increase your chances of eventual success in your formulation development. Variable density extrusion should be considered at the same time as die hole diameter.
- The importance of this may not be immediately relevant but without this ability being available to you now your options with different formulation ingredients or process parameters you may want to (or must) use in the future may be reduced.
- It makes sense to plan for this before the purchase decision is made.
- There are other factors that also influence final pellet diameter (but none as critical as the relationship between the hole diameter and depth).
- Water content can also have an influence. On drying, pellets can shrink as they lose water. The shrinkage can vary depending on the density of the pellets and the properties of the material used in the formulation. Some formulations can be up to 50% water. The higher the water content, the higher the potential for shrinkage upon drying, thus a 1 mm wet pellet may significantly decrease in volume, and therefore diameter, or density (and therefor physical properties), during the drying process.
- If the shrinkage is directly related to the loss of water content and no additional air spaces are created then the diameter could reduce from 1.0 mm to approximately 0.88 mm diameter (approximately a 30% reduction in volume). In practise this means that we may expect a reduction in diameter of 5 to 10 % for very moist formulations. A formulation with a lower water content, mixed with a variety of excipients and additives might see a smaller percentage of shrinkage.
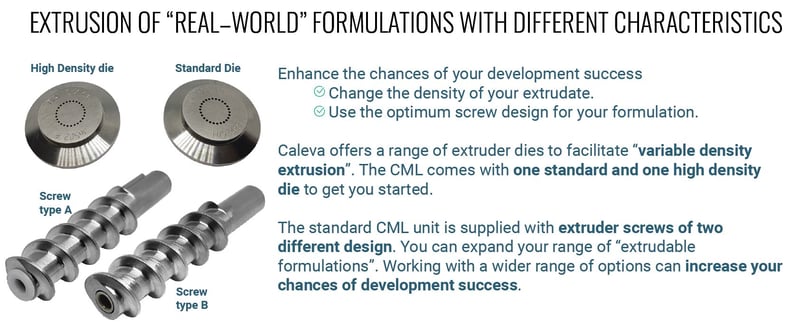
- You should give yourself the ability to experiment using dies with a different diameter to depth ratio at an early stage of product development. First choose the target size pellet, for example 1 mm, then consider a die that has holes with a 1 mm diameter. This should give you the size range that you are looking for. Some adjustment may be necessary for your formulation, but this is a good starting point. Changing the diameter of the die hole (at an early stage of development) and also the relation between the hole size and its depth is much simpler than continually changing your formulation or operating parameters to suit inflexible equipment.
- Caleva design and manufacture a range of different extruders offering dies with holes from 0.5 mm up to 8.0 mm in diameter. Depending on the diameter, hole depths can be from 0.5 mm up to 32 mm. Dies are also available in a variety of shapes (such as trilobe and quadrilobe/quadralobe) to increase the surface area of the extrudate for a given weight of material.
- If you want to increase your chances of development success and you are thinking about extrusion or extrusion and spheronization and would like more information about the ideas presented above we will be happy to discuss your program and advise on what may be your best way to go forward. Please contact us.
The variable density range:
Leave A Comment